WATER COOLED CABLES
Specifications, Features, Information, Data steets and Selection of Water Cooled Cables for your EAF
Features
General Features
The electric arc furnace secondary electrical circuit consists of several components including the
delta closure secondary circuit, water cooled cables, electrode arms, and the electrodes.
The water cooled cables
are the only flexible part of the secondary electrical system. These allow for raising,
lowering and swinging of the electrodes. Furnaces usually operate with between two and four cables per phase.
The water cooled cable generally consists of multiple copper wire strands which are soldered or crimped to copper terminals at either end of the cable.
The copper cable is covered with a rubber hose which is secured at the terminals with nonmagnetic stainless steel bands.
Main parameters
Main parameters for the water cooled cables sizing are the following:
1. Current density
Suggested max value of the current density in a water cooled cable is 4,5 A/mm2 for EAF and 5,5 A/mm2 for LF.
2. Water cooling flow rate
Water cooling flow rate is calculated according to current intensity, inlet and outlet temperatures.
3. Bending radius
The minimum bending radius of the cable is around normally 5-6 times the inner diameter of the water hose
4. Cable length
The cable length is determined to allow raising, lowering and swinging of electrodes.
How it Works
How it's made (see below)
How it's made
The water cooled cable generally consists of multiple copper wire strands which are soldered or crimped to copper terminals at either end of the cable.
The copper cable is covered with a rubber hose which is secured at the terminals with nonmagnetic stainless steel bands.
Copper terminals
They are made of machined high conductivity copper. Cast terminals are not suggested.
Copper ropes
Copper ropes are manually covered a punched rubber sleeve on half of the copper ropes only.
Recent development with the new technology Punch and Press Technology (P&P Tech) have already proven than the extruded and punched copper ropes
on all copper ropes gives better results and performances granting more copper ropes protection, mechanical stress distribution, improved strength against flexion and torsion and less cable movement.
Connection of copper ropes to terminals
They are 2 different technologies to fix ropes to terminals:
- Soldering: process that requires a pre-heating causing flexibility deterioration on copper ropes
- Crimped : no pre-heating --> Suggested
Inner core
A central rubber pipe is normally supporting the copper ropes. Metal supporting spring solution to be avoided.
Outer rubber hose
Outer hose need developed in order to have good performances against abrasion, torsion, flexion, high temperatures and chemical resistance.
How it should NOT workPoor design and quality of water cooled cables may cause huge problems to EAF in terms of efficiency, productivity, and safety.
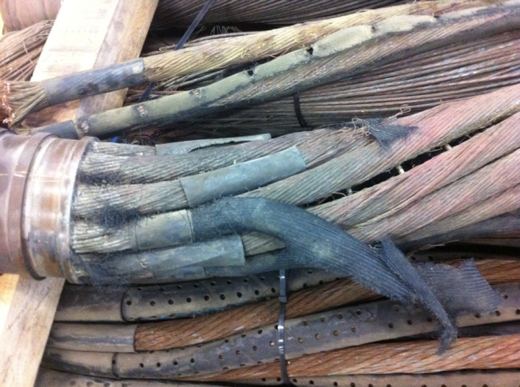
Bad Example 1:
Bad quality rubber sleeve which deteriorated quickly, causing water cooling flow circulation stoppage.
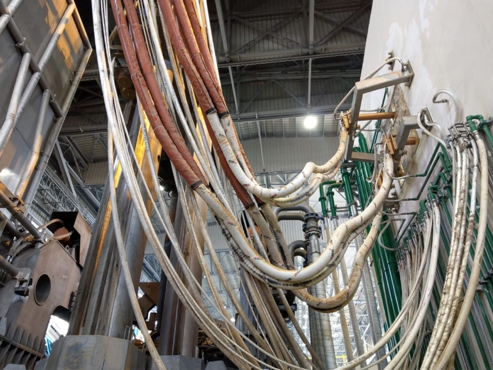
Bad Example 2:
Too hard and rigid outer rubber hose in consideration of the swivelling angle of electric arc furnace.
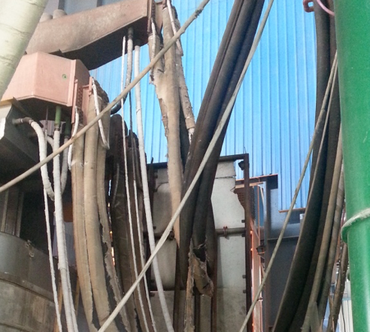
Bad Example 3:
Under-estimation of electrodynamic forces generated by high current magnetic fields.

Bad Example 4:
Internal core made of a metal spring caused huge friction and abrasion against copper ropes